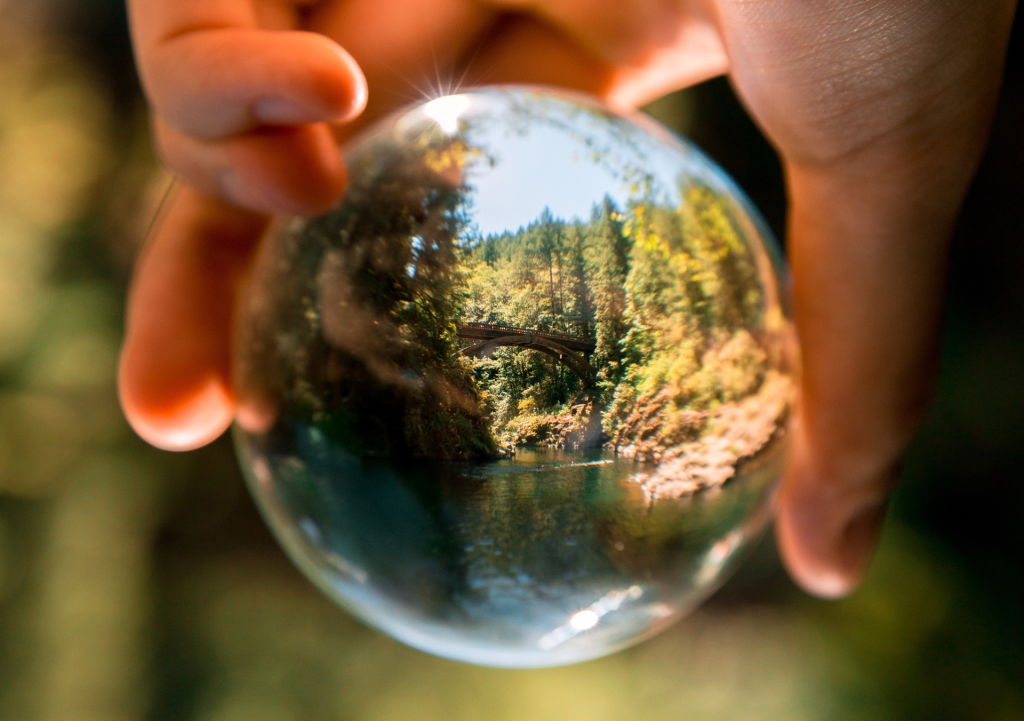
Plastic waste is a notorious and growing problem around the globe, and with this problem, has emerged a pressing need for innovation. The flexibility of plastics that can be used repeatedly is invaluable to addressing this problem.
In the fast-moving world of production, thermoplastics offer a clever and modern solution to the modern problem of excessive waste. These plastics can be recycled and reused in multiple parts.
What Are Thermoplastics?
Thermoplastics are a popular manufacturing material that continues to rise in the eyes of engineers and designers across the world due to some unique attributes. Thanks to their chemical makeup, thermoplastics can be heated and molded into any shape over and over again without sacrificing appearance or material integrity. Unlike thermosets, there is no chemical bonding during the curing process. This not only means that they’re well suited to an endless list of design possibilities, but also that they are functionally recyclable.
That unique characteristic can help you reduce waste and even reduce cost. Their meltable, moldable nature means that they can be re-used multiple times in new applications.
How Thermoplastics Can Help Your Projects Stay Environmentally Friendly
1. Thermoplastic Recycling
Thermoplastics have a variety of appealing characteristics: resistance to damage and corrosion, high strength, low density, and beyond. But environmentally speaking, their real game changer is their reusability. Thermoplastics can be recycled into other shapes and forms using heat, and this can be done over and over again.
⇨ Read Now: The Advantages of Thermoplastics
Thermoplastic recycling is made possible due to the weak attraction of the comprising molecules. Where some plastics form strong bonds when heated, thermoplastics stay formable and flexible whether you use them twice or over ten times, which makes thermoplastic recycling a powerful tool in any engineer’s arsenal. Using recycled thermoplastics also has a great impact on part cost as well!
2. Heat Resistance
Thanks to some of the same properties that make thermoplastic recycling a possibility, many thermoplastics are also largely fire retardant. As noted above, high heats cause thermoplastics to melt instead of burn, and ultimately, resist ignition for longer. For clients, this means that thermoplastics create products that are more resistant to accidental damage or heat-related failure. Even in the case of ignition, many thermoplastics are capable of self-extinguishing due to a high chlorine content. These factors in tandem reduce risks of environmental contamination from smoke, waste due to accidental loss, and the need to replace parts with virgin or unused plastics.
⇨ Read Now: Why Thermoforming Polymers Are Sustainable
Some materials appear recyclable on the surface, but when exposed to a heat beyond their ignition point, they go up in flames, giving off toxic fumes and dioxins. Industrial Custom Products can source nontoxic materials that are not a threat to the environment thanks to insignificant dioxin output during burning. This means that even if the worst happens and unintended burning occurs, you’ll still be mitigating the environmental impact.
Choosing thermoplastics and utilizing thermoplastic recycling is a modern way to further your design concepts. Industrial Custom Products offers a variety of tools and methods for producing the parts that you envision for the projects that you care about. Contact us and speak with an engineer about your project at (612) 781-2255, or request a quote online. You will receive a prompt response.
Industrial Custom Products is a one-stop-shop for custom manufacturing and plastic fabrication, including: prototyping and product development, die cutting and dieless knife cutting, thermoforming and vacuum forming, large part thermoforming, CNC plastic routing, fabrication and assembly and drape forming.