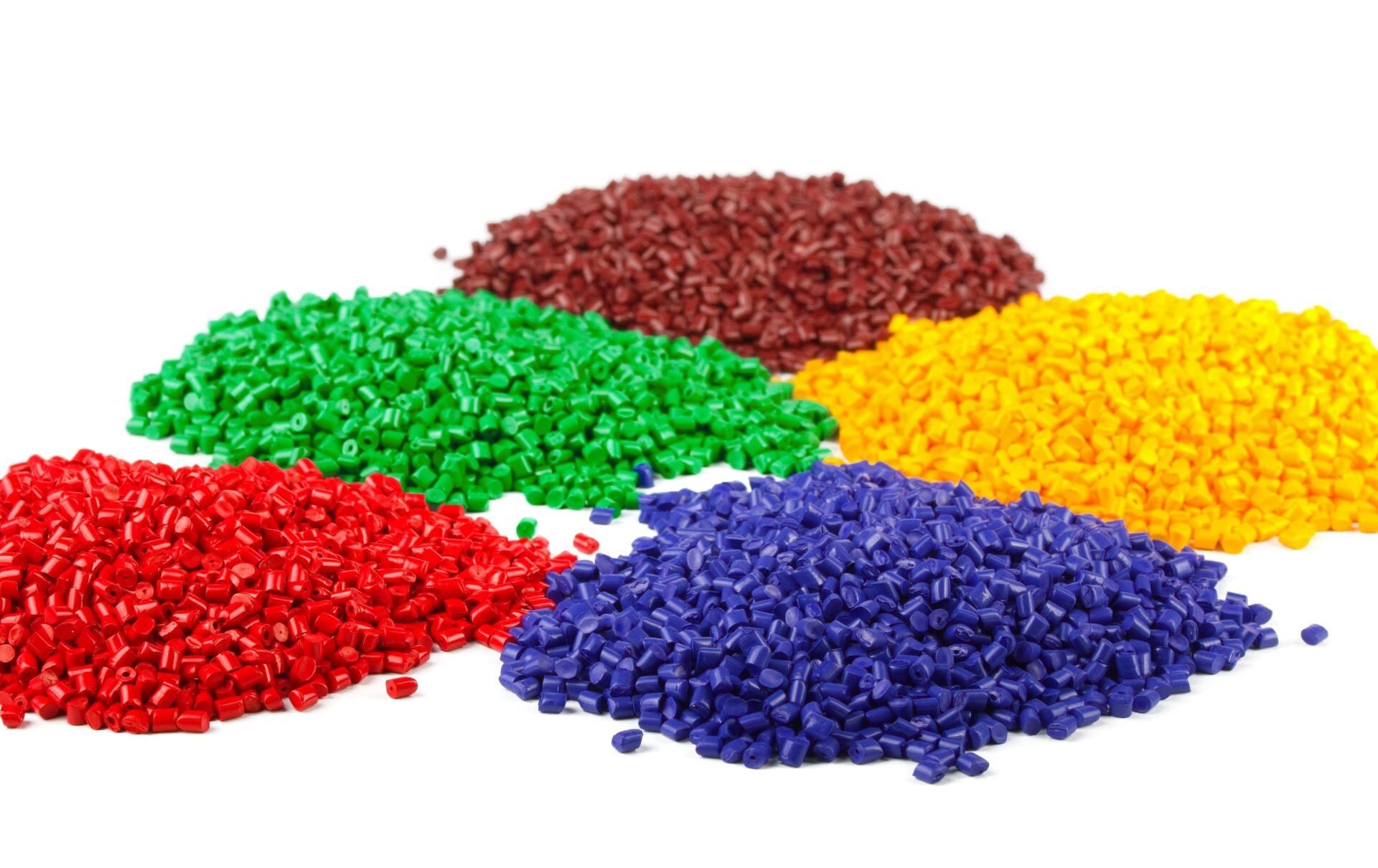
Thermosets vs. Thermoplastics: Understanding the Advantages of Each
Many manufacturers have already turned away from pricier metal options to use high-quality plastics. When choosing plastics for fabrication, there are two primary plastics of choice: thermoplastics and thermosets. Both thermoplastics and thermosets come with inherent characteristics that make them well-suited to a huge variety of products in the world of manufacturing and design.
But which one is better?
That’s typically the question designers, engineers and project managers will ask, but it’s not a question with an easy answer. “Better” depends on the application of the completed part, the conditions it will be subject to and the overall goals of the project.
The best way to determine the better option for your project is to understand Understanding the major differences between the material types gives project managers a significant advantage during the early stages of the development process.
At Industrial Custom Products, we offer material guidance as well as manufacturing capabilities for plastic and flexible parts. Let’s break down what thermoplastics and thermosets are, and the advantages/disadvantages of both options.
What Are Thermosets?
Thermosets are a series of polymers that are cross-linked together to form an irreversible chemical bond. They are able to achieve thermal stability following a single curing process. Thermosets are sturdy, difficult to deform, and may be a strong choice for environments with extreme or variable temperatures.
However, for the same reasons as their advantages, thermosets are also poor thermal conductors, can be brittle and difficult to surface finish, and can fail when exposed to heavy vibrations or other areas that impact its rigidity.
Advantages of Thermosets:
- High strength-to-weight ratio and performance
- High dielectric strength
- Low thermal conductivity and microwave transparency
- Corrosion-resistant
- Water-resistant
- Lower tooling/set-up costs vs. thermoplastics
Disadvantages of Thermosets:
- Cannot be recycled
- Cannot be remolded or reshaped
- Poor thermal conductivity
- Rigidness of material can cause product failure in high-vibration applications
Thermosets are the better choice for parts that need to retain their shape under heat, water and conductivity.
What Are Thermoplastics?
Thermoplastics are a popular manufacturing material that continues to rise in the eyes of engineers and designers across the world due to some unique attributes. Thanks to their chemical makeup, thermoplastics can be heated and molded into any shape over and over again without sacrificing appearance or material integrity. Unlike thermosets, there is no chemical bonding during the curing process. This not only means that they’re well suited to an endless list of design possibilities, but also that they are functionally recyclable.
That unique characteristic can help you reduce waste and even reduce cost. Their meltable, moldable nature means that they can be susceptible to deformation in high temperatures, but in stable environments, thermoplastics shine.
Advantages of Thermoplastics:
- Recyclable
- Can be remolded and reshaped without losing material integrity
- Can be used for assembly with metal, other plastics, flexible materials, etc.
- Impact-resistant
- Corrosion-resistant
- Chemical-resistant
- Slip enhancement
- Chip resistant
- Electrical insulation
Disadvantages of Thermosets:
- Tend to be costlier vs thermosets
- May melt if reheated, causing product failure
Thermosets are often the better choice for most part applications that will not be exposed to extreme heat.
Related Content: The Advantages of Thermoplastics
How to Choose Between Thermosets and Thermoplastics
Choosing between a thermoplastic and thermoset is highly dependent on the product application, surrounding materials and your overall budget.
At a high-level, if you need an extremely durable plastic product, choose thermoset; if you need something with flexibility and future re-use, choose a thermoplastic. However, not every product application will be that black and white.
Industrial Custom Products can help you select a fitting material and ensure a smooth and successful product development process. We can help you choose the best plastic based on your unique product needs.
For engineers and designers interested in utilizing plastics, send us your design questions to get a more solid recommendation.
Industrial Custom Products is a one-stop-shop for custom manufacturing and plastic fabrication, including: prototyping and product development, die cutting and dieless knife cutting, thermoforming and vacuum forming, large part thermoforming, CNC plastic routing, fabrication and assembly and drape forming.