Not all thermoplastics perform the same. Material selection is vital for any plastic part fabrication, to ensure a desired result.
ABS, HDPE and TPO are all “strong” plastic choices in different ways – whether it’s physically strong & stiff, resistant to corrosion, UV resistant or all of the above. In this article, we’ll compare these three common thermoplastics so you can determine the right choice for your project.
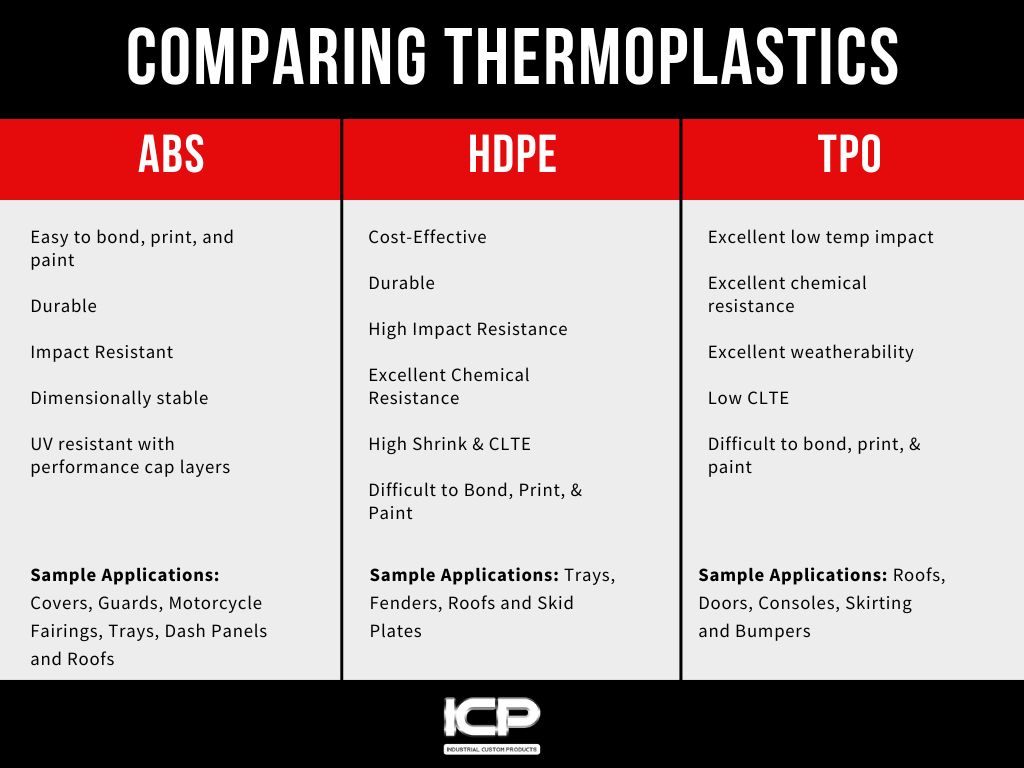
1. Acrylonitrile Butadiene Styrene (ABS)
ABS is a versatile plastic that’s ideal for applications where strength, stiffness and dimensional stability are important. For that reason, it’s a popular choice for the automotive, recreational vehicle and construction industries.
Properties
- Easy to bond, print, and paint
- Durable
- Impact Resistant
- Dimensionally stable
- UV resistant with performance cap layers
Sample Applications
- Covers
- Guards
- Motorcycle fairings
- Trays
- Dash panels
- Roofs
2. High Density Polyethylene (HDPE)
Polyethylene (PE) is one of the most commonly used plastics in manufacturing. It’s a rigid plastic resin with high chemical resistance. HDPE is a variation of PE that has an extremely high impact resistance and high tensile strength. It can also be recycled and used over again. However, because of that same recyclability, it’s best suited to low temperature applications.
Properties
- Cost-Effective
- Durable
- High Impact Resistance
- Excellent Chemical Resistance
- High Shrink & CLTE
- Difficult to Bond, Print, & Paint
Sample Applications
- Trays
- Fenders
- Roofs
- Skid Plates
3. Thermoplastic Olefin (TPO)
TPO is a combination of polypropylene, elastomers and mineral fillers offering a unique balance of stiffness and thermal expansion. TPO has superior weather-ability so it does not require a cap and it ranks extremely high on impact and chemical resistance. TPO can be easily customized with color, finish and adhesives. This makes it a popular choice for automotive and recreational vehicles for exterior applications.
Properties
- Excellent low temp impact
- Excellent chemical resistance
- Excellent weatherability
- Low CLTE
- Difficult to bond, print, & paint
Sample Applications
- Roofs
- Doors
- Consoles
- Skirting
- Bumpers
Related Content: TPO Features & Benefits in Thermoforming
Choose the Right Material with ICP
Since 1955, ICP has grown to become an award-winning leader in prototyping, developing, and manufacturing high-quality plastic and flexible products. The foundation of our company is our absolute, unyielding commitment to high-quality work and on-time delivery.
Contact us and speak with an engineer about your project at (612) 781-2255, or request a quote online. You will receive a prompt response.
Industrial Custom Products is a one-stop-shop for custom manufacturing and plastic fabrication, including: prototyping and product development, die cutting and dieless knife cutting, thermoforming and vacuum forming, large part thermoforming, CNC plastic routing, fabrication and assembly and drape forming.