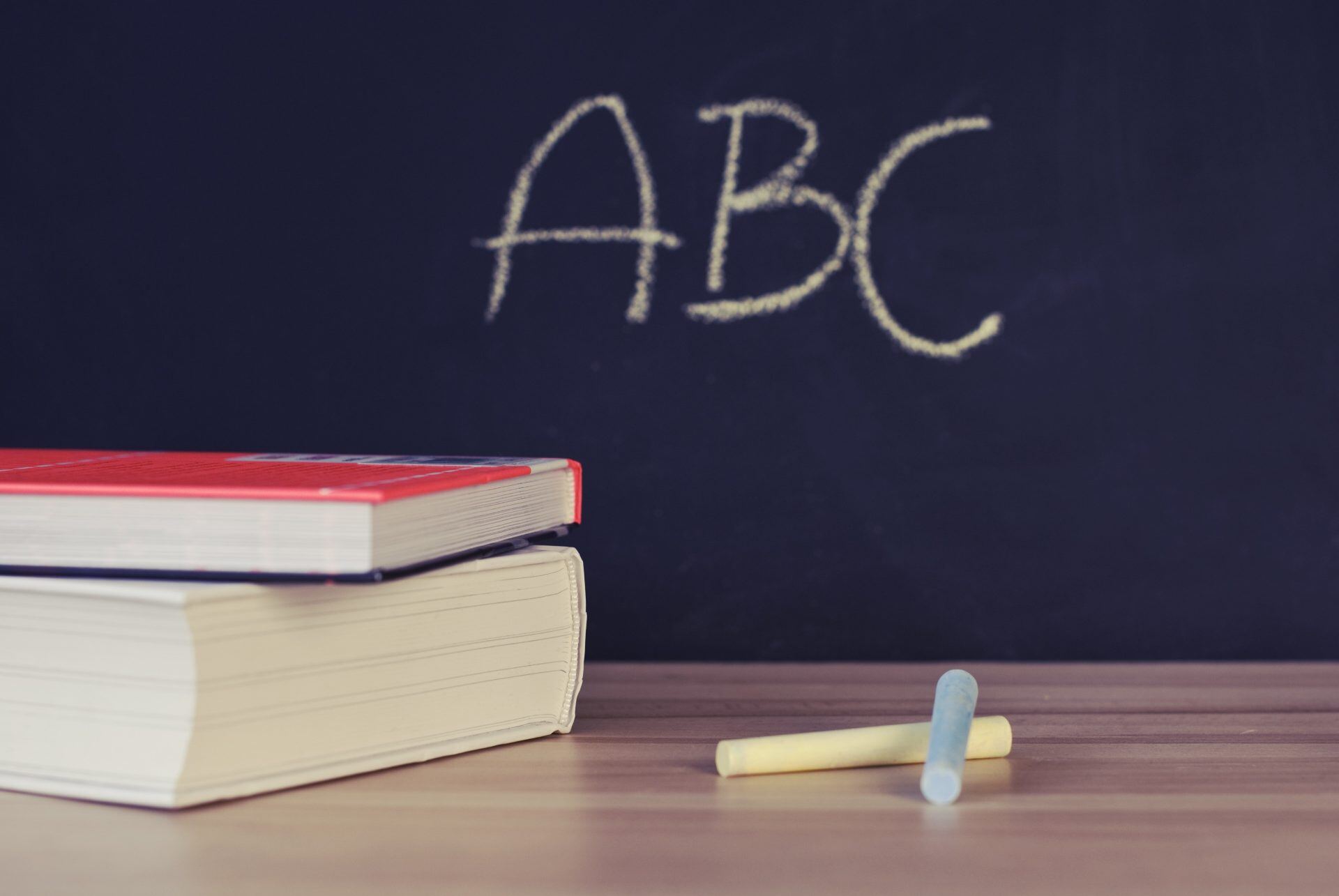
Thermoforming Design Basics
Thermoforming can be a very cost-effective means of production for precision parts where tooling costs would be excessive. Knowing the basics is critical for ensuring manufacturability and cost efficiency at each stage of the process. Use this guide to understand the critical terms and considerations to be made at each stage of the thermoforming design and creation process.
Note: The below design guidelines are general in nature as each part is unique and may or may not be able to live outside these parameters. This is a reference guide for engineers, procurement specialists and sourcing specialists who are new to thermoforming.
How Thermoforming Works
As a precursor to the following design basics: here’s a refresher on how the thermoforming process works. Flat sheets of thermoplastics are heated to a pliable temperature, then molded to a tool shape using suction from a vacuum. The final pieces can be hand trimmed or trimmed with a multi-axis CNC.
This process means lower tooling costs and shorter lead times, which makes it very cost-effective for lower-volume and larger parts.
Related Content: Thermoforming in a Nutshell
Thermoforming Design Terms
Draft
The degree of taper on a vertical sidewall. This assists in the removal of the part from the mold once the part is formed. Three degrees of draft will ensure that there is ease of removal of the tool; however, if your requirements are less than that, please consult with us.
Draw
This refers to the action of the thermoplastic drawn into the mold.
Draw Ratio
The ratio of the horizontal dimension versus the vertical dimension. We strive for a 2:1 draw ratio to allow the material to flow without substantial thinning that may weaken the part. If your requirements differ from that, please contact us to discuss. The type of thermoplastic used and thickness will impact that draw ratio.
Radius
The radius refers to the area at the bottom of the draw. The greater the radius, the more even the material distribution will be.
Related Content: Troubleshooting the Thermoforming Process
Part Dimensioning & Reference Points
All dimensions given should be relative to the tool side of the part. Reference points should be designed so that all measurements are relative to a controlled surface.
Undercuts/Breakaways
An undercut is often used in injection molding – and is a recessed grove that allows a part to be removed from the injection mold without damage. Those new to thermoforming often ask about undercuts, but they are not necessary with this process. We can accomplish the same effect through the use of movable components in the mold, also called breakaways. This will dramatically increase the price of the tooling, so please consult with us prior to finalizing the print.
Tolerances
Tolerances help determine how exact the measurements must be in order to prevent product failure and to best accommodate different materials during the vacuum forming and thermoforming process. Thermoformed parts are either hand-trimmed or trimmed with one of our 3-Axis or 5-Axis CNC trimming machines depending on tolerances and overall functionality of the part. Our standard tolerance sheet is available upon request.
Related Content: The Ins and Outs of Thermoforming Tolerances
Texture
Texture should be incorporated into the part in either the tooling or the sheet in order to hide vacuum holes, scratches, etc. It can also be used as a part of the design process, to add aesthetic and/or practical applications to the completed part. The texture is generally put into the sheet but can also be put into the mold. Contact us for the proper texture recommendation for your part.
Related Content: Maximize Your Design With Thermoforming Textures
Color
From simple color selections to elaborate designs, thermoplastics shine where creativity thrives. With thermoplastic design, you can color-match to previous designs or create something entirely new. Color and design are only as limited as your imagination.
Related Content: The Power and Possibilities of Color in Thermoplastic Design
Knowing these key terms and following the guidelines above will ensure a part that’s easy to manufacture and within your budget.
Thermoforming with ICP
Since 1955, ICP has grown to become an award-winning leader in prototyping, developing, and manufacturing high-quality plastic and flexible products. The foundation of our company is our absolute, unyielding commitment to high-quality work and on-time delivery.
Contact us and speak with an engineer about your project at (612) 781-2255, or request a quote online. You will receive a prompt response.
Industrial Custom Products is a one-stop-shop for custom manufacturing and plastic fabrication, including: prototyping and product development, die cutting and dieless knife cutting, thermoforming and vacuum forming, large part thermoforming, CNC plastic routing, fabrication and assembly and drape forming.