Choosing the right production method for your plastic part is more involved process than it seems on the surface. With all the options out there, it can be hard to know what to choose. And selecting an inefficient production method can result in lost revenue, delays, or inadequate results.
Two of the most common plastic production options for repeat parts are rotational molding and thermoforming. This blog will break down the difference between the two, so you can easily decide the right method for your projects.
Rotational Molding
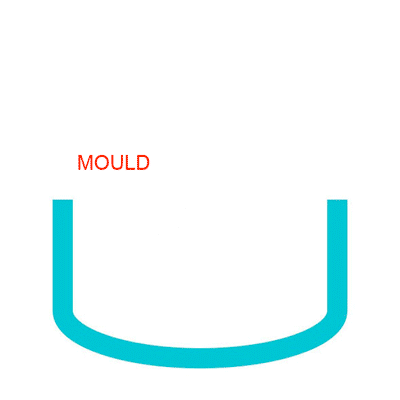
Rotomolding, or rotational molding, is a process that utilizes hollow molds, powder resins, heat, and steady rotation. The powder resin is heated until it melts and then the mold is carefully rotated until the liquid coats the entire interior. Once this is completed, the mold is cooled.
When to Choose Rotomolding
Rotomolding is especially effective when utilized to form plastic storage tanks and other large-scale hollow containers. This method is ideal for these types of projects as the materials conducive to rotomolding are suitable for storing wastewaters, chemicals, fuels, oils and more. Combining high-quality, versatile materials with the rotomolding process yields multilayer, hollow parts that require zero welding and no subsequent joining.
Thermoforming
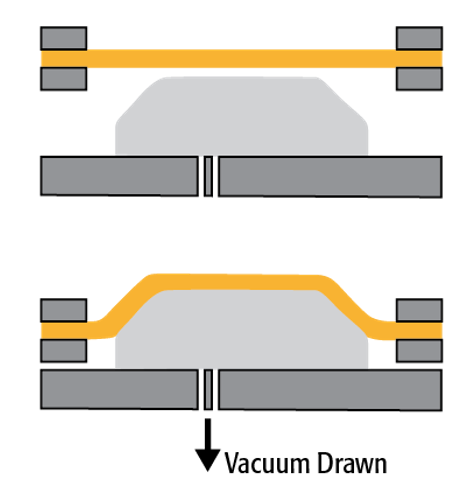
The thermoforming process works by heating, molded, and vacuum-forming sheets of thermoplastics and then trimming the excess. The cost of thermoforming is often lower than that of rotomolding as the tooling tends to be less expensive and the cost of parts lower. Thanks to advanced machining, the thermoforming process can also handle larger items, tighter tolerances, and efficient production. Plus, thermoforming is suited to a wider range of potential production materials that can be selected to best support any design.
When to Choose Thermoforming
Both methods offer specialty plastics forming, but for larger projects or projects that would benefit from specialty or high-color materials, thermoforming generally offers more possibilities than rotomolding. Rotomolding is durable but thermoforming is better suited for detail work or projects that require flexible tooling.
In short, thermoforming is best for repeat part production and/or parts that require precision and detail.
If you’re not sure which methodology best supports your project needs, consulting with a plastic production professional can guide you toward the solution that suits your needs.
Industrial Custom Products has decades of experience in a variety of industries using many different materials, processes, and technologies.
If you’re looking for the right plastic molding for your design concept or project, Industrial Custom Products has the thermoforming services you’re looking for. Contact us and speak with an engineer about your project at (612) 781-2255, or request a quote online. You will receive a prompt response.
Contact Us for a No-Obligation Quote
Industrial Custom Products is a one-stop-shop for custom manufacturing and plastic fabrication, including: prototyping and product development, die cutting and dieless knife cutting, thermoforming and vacuum forming, large part thermoforming, CNC plastic routing, fabrication and assembly and drape forming.